Silga’s Anodizing division performs anodizing treatments on various types of aluminum, normal, neutral and hard oxidation, chromate and passivation treatments, treatments of electrolytic brightening and acid satining, chemical and electrolytic coloration, for an amount of over 80 finishings.
The division has 10 work units and uses a multi-program automatic, managed with an innovative software for frame processing, which allows the standardization and repetability of processes. The inbound material is encoded, for part number, quantity and code processing, ensuring traceability throughout the industrial flow, from arrival to final delivery to the customer.
The strengths of the department are quality of processing and its high flexibility which allows it to adapt its treatments, decorative and technical, to any type of hardware and die casting used in various sectors such as automotive, machinery, fixtures, screws, clothing, shoes and leather goods.
Plants and materials
The anodic oxidation division has an automatic and multi-program plant with material advancement in self-management by an innovative software that allows to monitor and manage continuously temperatures, times and current of the processes, in addition it ensures the progress of production orders.
The daily productivity is 20,000 sdm/day, with maximum dimensions of manufactured 200 x 95 x 50 cm.
Here below the materials we can treat
Aluminium and aluminum alloys
- group 1000 (Aluminum): they are pure aluminum alloys with excellent attitude to anodic oxidation (standard and hard) and colouring and good resistance to corrosion;
- group-2000 (alloys Al – Copper) called AVIONAL: they are alloys with middle characteristics of anodic oxidation (standard and hard) and colouring and good resistance to fatigue;
- group 3000 (alloys Al- Manganese): they are aluminum alloys with good characteristics of anodizing (standard and hard) and colouring;
- group 4000 (alloys Al- Silicon): they are casting alloys with middle characteristics of anodizing (standard and hard) and colouring;
- group 5000 (alloys Al – Magnesium) called PERALUMAN: they are alloys with good characteristics of anodizing (standard and hard) and colouring and good resistance to corrosion, showing qualities of good workability;
- group 6000 (alloys Al – Silicon and Magnesium) called ANTICORODAL: they are aluminum alloys with good characteristics of anodizing (standard and hard) and colouring and good resistance to corrosion;
- group 7000 (alloys Al – Zinc and Magnesium) called ERGAL: they are aluminum alloys with good characteristics of anodizing (standard and hard) and colouring, with high structural force.
Aluminum die cast alloys
They are aluminum alloys obtained by die cast containing specific metals, in variables percentages, such as silicon (Si), copper (Cu), iron (Fe), magnesium (Mg) and Tin (Sn), which ensure to the manufactured specific characteristics. The die-cast alloys anodizing, the strength of SILGA S.p.A., involves a series of technical and engineering solutions to ensure proper and quality products.
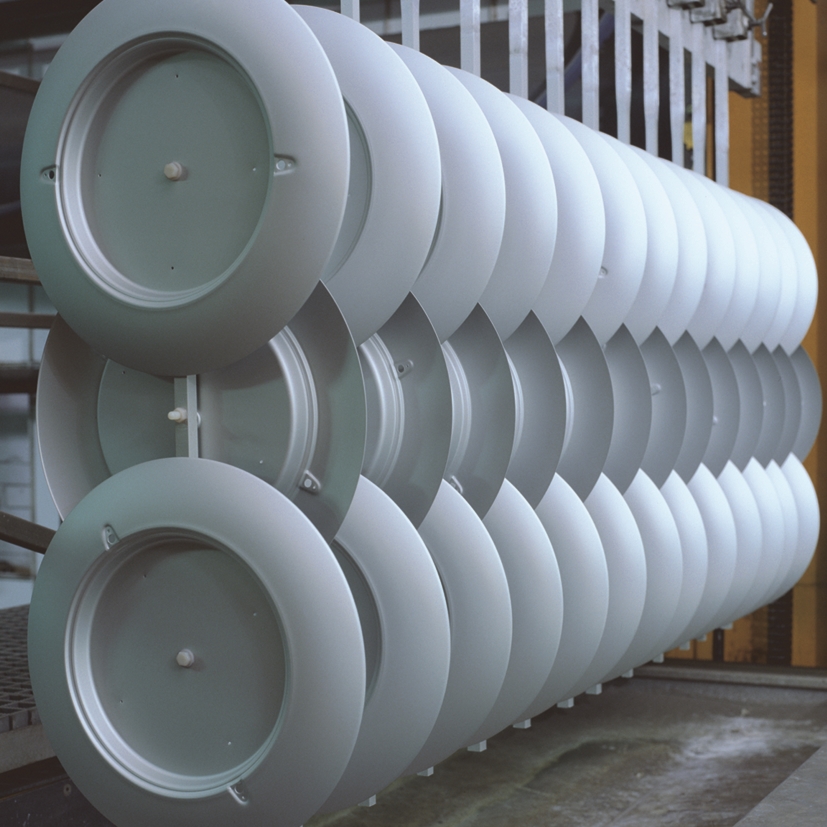