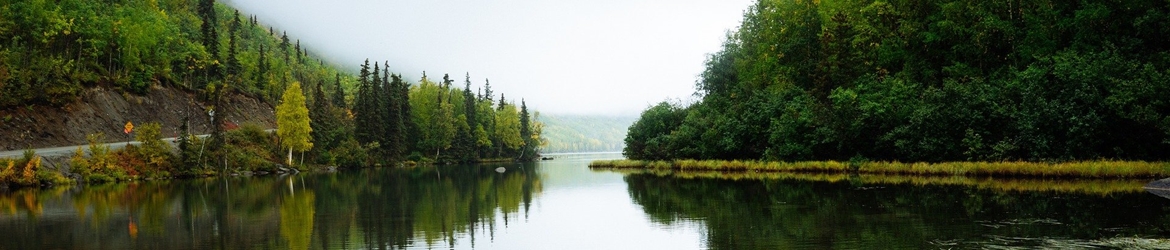
Silga S.p.A. is determined to ensure a balance between the company’s aims and the safeguard of the health of people and more generally of the surrounding environment.
For this reason, the company has established a Safety Management System inspired on standards of the European Directives 96/82/CE and 2003/105/CE. It also has a long-standing integrated Quality Management and Environment System in accordance with the Standard UNI EN ISO 9001:2015 and on Standard UNI EN ISO 14001:2015.
Silga S.p.A. therefore undertakes to ensure compliance with current legislation, both environmental and safety and health in the workplace (such as, REACH, RoHS, D. Lgs. 81/2008 and D. Lgs. 105/2015) and to provide adequate resources to ensure technical, organisational and managerial interventions in order to reduce environmental impacts in accordance with ergonomic principles and always with an eye towards a continuous improvement.
Plants
The company has two chemical-physical purification plants, technologically advanced, with supervision and remote control systems and, since 2019, a new biological purification plant has been realized and implemented always with supervision and control systems, according to the criteria of ‘Industry 4.0’, which both improves the environmental performances of industrial wastewater concerning nitrogen and ammonia nitrogen parameters and allows the recovery of about a 10% of the purified wastewater with a saving of the precious natural resource.
The two production sites have two cogeneration plants, one with a potential of 600 kwe and the other with a potential of 420 kwe. These plants allow the self-production of electricity and heat with a significant savings of natural and economic resources. In the two sites there are also two photovoltaic plants, one with a potential of 458,85 kwp the other with a potential of 200 kwp, which contribute to what already produced by the cogeneration plants.
Since 2016, Silga has implemented an Organisational Model in accordance to Decree Law No 231/2001 and it has established an External Supervisory Body and a Code of Ethics.
Finally, there is in the company a post-combustion system with methane burner type B-01 maximum with capacity of 87,000 kcal/ h used for the abatement of solvents emitted in the air (SOV) in rotobarrel painting plants of the Galvanic Division that allows a reduction of 80% more than the limit required by law.